Guidelines for complying with UL safety standards and ensuring A2L system safety in commercial refrigeration applications
By Joe Summers, senior product manager – scrolls & drives, Copeland
The transition to lower-global warming potential (GWP) refrigerants is accelerating rapidly in commercial refrigeration equipment. Among the emerging alternatives, A2L refrigerants are poised to play broader roles in both self-contained and remote system architectures. Available in a variety of GWP ratings below 150 and 300, A2Ls can help equipment manufacturers and end users meet the Environmental Protection Agency’s (EPA) GWP limits across key sectors. But with the “lower flammability” A2L classification, they also introduce new safety considerations and risk mitigation measures for application, equipment and component design.
Ensuring electrical system safety compliance is among the key design considerations with A2L-optimized equipment — as powered electrical components could be a potential ignition source upon contact with a flammable concentration of gas. The Underwriters Laboratories (UL) 60335-2-89, 2nd edition safety standard provides guidelines for the safe use of flammable refrigerants in refrigeration equipment, including considerations for electrical components.
UL 60335-2-89, 2nd edition includes provisions for equipment safety when using highly flammable A3 and mildly flammable A2L refrigerants. It specifies A2L charge limit allowances, leak rates and detection requirements in addition to design strategies with consideration of an A2L’s lower flammability limit (LFL). Because electrical sparking or charges could be potential sources of ignition, original equipment manufacturers (OEMs) must certify electrical componentry for safe use per applicable testing procedures and safety clauses.
Examples of electrical componentry found within compressors and condensing units include:
- Relays/contactors and/or devices used for switching electrical currents on/off
- Controllers
- Variable frequency drives (VFDs)
- Electrical enclosure (box) within which a full system may be contained
Note: LFL is based on the worst-case formulation (WCF) — or maximum refrigerant burning velocity — of all A2L refrigerants being considered for approval.
Safety certification design strategies
From a high-level perspective, UL 60335-2-89, 2nd edition delineates two types of systems in considering the measures required for ensuring refrigeration equipment safety certification when using A2L refrigerants: protected and unprotected systems.
- Protected systems are those in which no part of the cooling system is inside the food storage compartment — such as remote architectures — or where any part of a cooling system is enclosed in such a way that the flammable gas cannot leak into the food storage space. Per Clause 22.111, appliances with a protected cooling system which use flammable refrigerants must be constructed to avoid any fire or explosion hazard in the event of refrigerant leaks.
- Unprotected systems are appliances in which at least one part of the cooling system is placed inside a food storage compartment or those which do not comply with Clause 22.111.
For unprotected systems, A2L safety compliance and/or certification may be achieved either through individual component-level certification or at a higher level that encompasses the entire system in an electrical enclosure. Only one certification approach is necessary to achieve compliance, and Copeland is currently qualifying its electrical components for individual certification.
Individual component-level certification
Per UL 60335-2-89, Annex 101.DVL, electrical components, relays or devices used on appliances designed for A2Ls must adhere to tight enclosure tolerances. These requirements are also in accordance with UL 60079-15 standard (Clause Annex BB) for non-sparking electrical apparatus.
In essence, the maximum size of openings — physical gaps (i.e., holes) in a device’s enclosure in which air could enter and/or fire could escape — must be limited as to prevent flame propagation to the outside. Thus, even if a device is sparking and/or has ignited on the inside, flame will not escape or propagate outside of the component.
Annex 101.DVL defines this opening as the effective diameter — which is the equivalent diameter of the opening of relays and similar components — via the following calculation:
deff = 4 × (A/S)
- deff is the effective diameter in mm
- A is the cross-sectional area of opening in mm2
- S is the length of the perimeter of the opening in mm
Thus, relays and similar electrical components are not considered as potential ignition sources if the effective diameter of all openings complies with the following calculation:
deff < 22.3 × Su-1.09 (in mm) ≥ 7 mm
- deff is the effective diameter in mm
- Su is the burning velocity in cm/s
Relays and/or switching devices: Certification exceptions
Per UL 60335-2-89, 2nd edition, Clause 22.111.1DV, certain relays and/or switching devices which are not considered an ignition source are deemed inherently “safe” and do not need to be tested for compliance with the UL standard. To qualify for this exception, these devices must meet the following criteria:
- Capable of 100,000 cycles, per Clause 24
- The switched electrical load (Le) in kVA is less than or equal to:
o Le = 5 × (6.7/Su)4 when breaking all phases (~66 kVA)
o Le = 2.5 × (6.7/Su)4 when breaking two legs of a three-phase load, or when breaking one or two legs of a single-phase load
where
o Le is the switched inductive electrical load in kilovolt amperes (kVA)
o Su is the burning velocity of a refrigerant in centimeters per second (cm/s)
See UL 60335-2-89, 2nd edition, Clause 22.111.1DV for more information on compliance measurement and testing.
Note: For Copeland’s A2L compressor optimization process, all on-board electrical components have been individually qualified under the UL 60079-15 standard. This gives OEMs the option to leverage pre-optimized compressors, rather than having to undertake their own compressor electronics qualification processes.
Electrical enclosure and/or system-level certification
For electrical enclosures, Annex 101.DVM provides a comprehensive range of testing requirements to certify that they comply with its flame-arrest enclosure verification standard. A flame-arrest enclosure is defined as a “device or assembly enclosing components with electrical contacts that are made and broken, or similar devices which can become a source of ignition”.
A qualifying enclosure must be able to withstand the internal ignition of leaked A2L refrigerant vapor, without suffering damage and transmitting flame to an external concentration of the same refrigerant. Note: qualified individual electrical components contained within a flame-arrest enclosure are not to be considered as sources of ignition.
If all openings in the flame-arrest enclosure comply with the Annex 101.DVM standard, the enclosure is considered compliant.
A2L safety compliance for variable frequency drives
Many OEMs are integrating variable-speed compression technology to improve system energy efficiencies, performance and reliability. The solution combines efficient scroll compressors with VFDs, which introduces another electrical component that must be certified for use in A2L refrigeration systems.
Per UL 60335-2-89, 2nd edition, VFDs are required to be certified to the UL 61800-5-1 standard. In addition to following the same testing 2-89 procedures for electrical components and enclosures, UL 61800-5-1 has specific spacing requirements for VFD components.
Copeland™ VFDs, EVM/EVH Series, are certified under this standard to meet applicable A2L qualification requirements for electrical components. In addition, select Copeland scroll variable-speed compressors are in the process of being optimized for use with A2L refrigerants. Production for A2L-optimized refrigeration compression models began in June 2023, and subsequent model releases will be staggered across all major product platforms in a timely and competitive manner.
Copeland VFDs utilize onboard relays that must be hermetically sealed and approved as defined in the UL 60079-15 standard. Additional common VFD components that could become potential sources of sparking — such as metal oxide varistors (MOVs) and transformers — must also be evaluated and modified to ensure fail-safe and/or non-sparking characteristics.
Surface temperature guidelines
Regardless of all other testing and certification measures, the surface temperature limits of affected electrical devices must also be factored into the A2L safety equation. Per Clause 22.114 in the UL 60335-2-89, 2nd edition standard, surface temperatures cannot exceed those defined in table 102.DV.
Copeland adheres to these guidelines for our own A2L electronic device certification processes.
Supporting our OEM partners
Copeland is committed to developing safe, A2L-optimized compression, controls and electrical componentry to help OEMs certify and complete their A2L equipment design cycles. Our individual components meet the certification requirements of UL 60335-2-89, Annex 101.DVL using the following A2L refrigerants: R-455A (146 GWP), R-454C (148 GWP), R-454A (238 GWP), R-32 (675 GWP) and R-454B (466 GWP). We have the application and engineering expertise — and flammable refrigerant testing facilities — to help OEMs maximize equipment safety using the next generation of low-GWP refrigerants.
To learn more about the safe use of A2L refrigerants in commercial refrigeration, please visit our website.
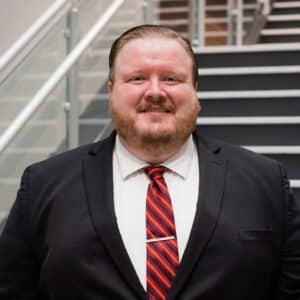
Author bio:
Working in collaboration with many of the highly skilled engineers at Copeland, Joe Summers leads new product development activities as the senior product manager for scroll and drives. In his role, he and his team develop variable speed compressors, variable frequency drives and low-power electronics focused on the cold chain. Joe has worked in the electro-mechanical engineering industry for over a decade. He earned a degree in electronics technology from Upper Valley Career Center, a bachelor’s degree from University of Toledo, and an MBA from the University of Dayton.