Featured in the September 2022 PBACCA Plenum Newsletter
Leak Detection
By Kelly McAnn, Florida Air Conditioning Apprenticeship Association Instructor
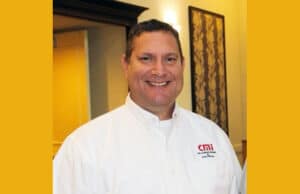
Today we are facing equipment and parts availability issues like we have never seen before. It is becoming more important now to find and repairs leaks. If replacement parts are not available and it’s not time for the owner to replace the system – it may be time to hone up on our repair skills. In this month’s article we’ll discuss how proper leak detection helps us make refrigerant circuit repairs.
First comes diagnosis; let’s be sure we are not going down the rabbit hole by chasing a leak that’s not there.
When you diagnose a system and see low pressure don’t automatically assume “low gas.” Check the subcooling and superheat. Remember to check both values even though it may have a TXV. Subcooling is used for charging; however, we use superheat to check txv and coil performance. After you have confirmed the low pressure is not due to a restriction etc… the first tool you should use is your eyes. Do a visual inspection, do you see an oil stain on the coil [as seen in the image] or at a braze joint? If the system is void of refrigerant you can pressurize with nitrogen, then look and listen for an obvious leak.
If no leak is found then it’s time to break out the leak detector. There are many types and brands of detectors but the procedures to use them are similar. Start by warming up and calibrating your electronic detector. You should start at the top working your way down, remember refrigerant is heavier
than air. Start your run over the likely spots: end bells of the coil, braze joints, fittings and flare fittings. Be cautious in the area around the service valves. Some techs fall into the “it’s the Schrader valve” trap; that’s not always the case. Keep your sensor moving slowly across the section you are searching? Leak detection becomes more of an art as you develop your strategies and procedures. It all comes with practice, keep it slow and be patient. Depending on the type of detector (ultrasonic types) it may be more critical to keep the sensor moving. When you get a light or sound indicating a presence of refrigerant its time to pinpoint the leak.
Change the sensitivity level on your detector or switch to soap bubbles to further pinpoint the leak. It may be necessary to move some of the aluminum fins out of your way. Next is the part where it may be a departure from previous thinking. In the past, when we’ve found a leak we think; time to change the “coil” without really pinpointing the leak. We will need a precise location to make a repair. Once located, clean the area and make the repair. Aluminum coils can be repaired as well, if you have not learned how to repair aluminum its nothing to be intimidated by. Although, it does require some instruction and practice but it can be repaired.
Depending on the leak location and type you may or may not be able to repair but I believe it’s worth the effort to get our clients cooling again. Some types of leak are not easily repairable; if you run across an “ants nest or champagne” leak it may be too extensive to repair.
If you cannot locate a leak with the two methods above you may need to do an isolation test, maybe the leak is in the lineset or somewhere you cannot access with a leak detector. As always make certain you are taking care of your tools, keep you leak detector clean, calibrated and serviceable. Replacing the sensor element and batteries as required. Please stay safe and hydrated!